How to improve SMT processing efficiency in PCBs factory
SMT production requires a variety of production and testing equipment, which is a multi process process.If the connectivity of each process is not strong, even a small error may cause the production line stop to running, which will not only affect the SMT processing efficiency, but also affect the product quality.The capacity of SMT is also the most important part to drive the operation of the whole PCBs factory. On the premise of ensuring the soldering quality of PCBs, if SMT processing is very efficient, it can also prove the overall strength of the factory. In such an important process, how can we improve the production efficiency of SMT?
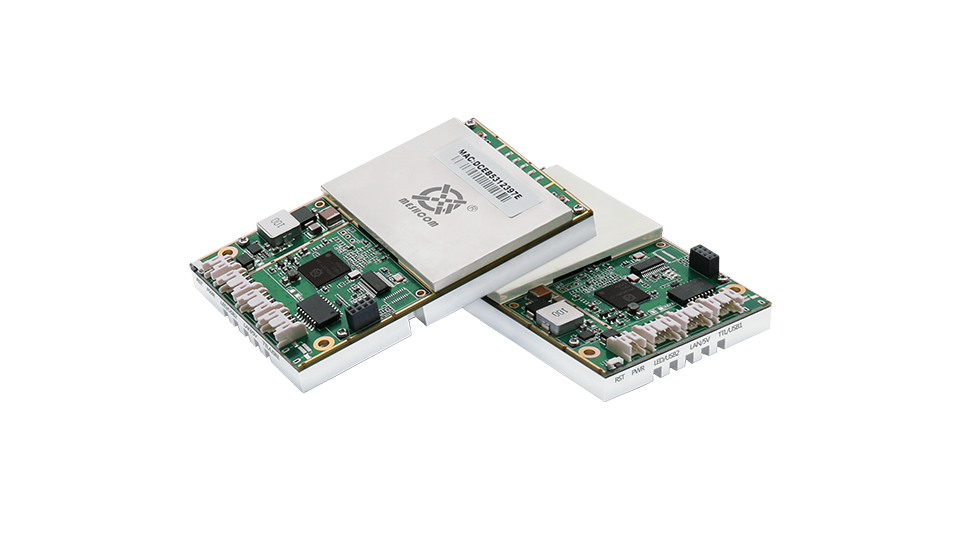
1) Producing preparation in advance
Since SMT is the first process in the production of PBCs, the cooperation of departments is one of the keys to ensure the improvement of SMT processing efficiency. The preparation items include the accurate output of production documents, the accuracy of component procurement, the accuracy of components inspection, material preparation, programming of the equipments, solder paste thawing, component baking, etc. These are preparations for work in advance, rather than implementation or confirmation in the actual production process. The problem points can be avoided outside the actual production and processing as far as possible, which also reduces the time for handling exceptions during online production, that is, improves the efficiency of SMT production. Whether the preparation work can be carried out well in advance is closely related to the management process of the factory.
2)Reduce equipment downtime
As mentioned above, we need to program the equipment in advance, which is directly related to the SMT processing efficiency. If you often go to the PCBs factory and observe carefully, you will find that many times the running time of multiple mounters in a production line is different. Even if it takes a few seconds to install a piece of PCBs, the whole order may take several hours or more to produce. In order to improve production efficiency, when editing the program, engineers must ensure that the running time of multiple mounters and other supporting equipment in a production line is the same. Reducing downtime is the most effective way to improve productivity.
3)Optimize equipment operation parameters
When optimizing the mounting procedure, optimize the synchronization rate of multiple mounting heads of the mounter to the highest, so as to reduce the times of changing the suction nozzle when the mounting head picks up the components and save the mounting time. The feeder with more picking times shall be placed on the feeding station near the printed board. During a picking and placing cycle, try to take materials only from the front or rear material station to reduce the moving distance of the mounting head. During each picking and placing cycle, make the mounting head operate at full load.
Visit our website for more information !
Article keywords :How,improve,SMT,processing,efficiency,PCBs,factory,SMT,